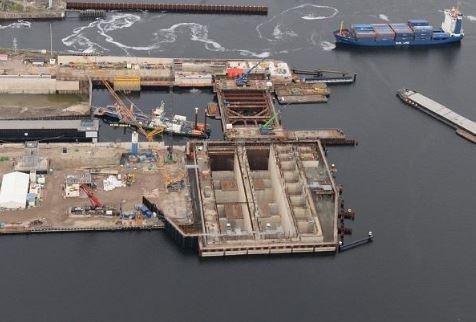
The inner lock head has been positioned in its exact position. Despite the gigantic size of the lock gate chamber, the sinking process has been done with great accuracy. Site manager Nikola Filipovic and Planner Dave Vermaas explained, “We have become much more experienced.”
Building Consortium OpenIJ has constructed the lock heads of the new sea lock by using the caisson method. The caissons – gigantic concrete structures – were erected in one go from ground level and were then subsequently sunk into the ground by mechanically digging the soil away from underneath the structures. “This method works much more efficiently and more cheaply than when large, deep excavation pits are used”, Nikola Filipovic explained. “In excavation pits you have to work in depth, length and width in phases because of the large number of struts – the beams of the framework that are needed to support the side walls of the deep excavation. That takes a lot of time. Using the caisson method is also an advantage for the environment as this construction method causes less noise nuisance because fewer piles have to be driven into the soil either by pile hammer or vibratory pile driver. Also, a sinking operation does not make any noise – the only sounds are those made by compressors and pumps. Ships have not at all been hindered by the construction and sinking activities.”
A caisson sinks under its own weight
“The sinking process can be compared to placing a paving stone for a paving”, explained Planner Dave Vermaas. “Placing that stone doesn’t work if there is too much sand under it. So, what you have to do is remove a handful of sand in the middle and it will be much easier to put that stone in place. No extra force like hammering is needed in the sinking process of the lock heads – they simply sink under their own (enormous) weight. The inner head weighs no less than 150,000 tonnes.” The sinking operation started with excavating a work space under the concrete structure. Access to the work space was through an opening in the floor. Filipovic explained, “Through this opening we brought the necessary equipment into the enclosed work space. Equipment such as water cannons to loosen up the soil, dredging arms to dredge away the loosened soil, install electric lights in the darkness under the floor to be able to inspect the caisson and the various equipment and the CCTV cameras. The CCTV cameras were used by the operators to remotely control the water cannons and dredging arms.”
Dry work space thanks to air pressure
The next phase was to enlarge the work space step by step. At some point in this process compressed air is needed. Vermaas explained why, “Think of the enclosed work space as an air cushion on which the concrete structure rests. The compressed air pushes the rising groundwater back into the soil. This keeps the workspace dry. Compare the enclosed work space with a glass that you push upside down into the water. The deeper you push that glass under water, the harder you have to push and the greater the air pressure in the glass. But the air remains in the glass.” By dredging away more and more soil from underneath the caisson, it started to sink under its own weight. During the sinking operation, so-called cutting edges under the caisson pushed the soil into the enclosed work space from where it was removed by the dredging arms. This process was constantly repeated until the caisson had reached its required final depth. The enclosed work space was now an empty space – only filled with compressed air. Vermaas explained, “We gradually replaced that air with concrete. While we poured concrete in on one side, the air escaped from the work space through small pipes. After the entire space under the caisson was filled with concrete, we released the air pressure. At that moment, the pressure of the ground water against the concrete structure created a new balance.”
Accurate work
The inner lock head reached its required depth on 9 October 2019. Filipovic explained, “This was the fourth caisson sinking operation for our team. We had already completed the sinking of the outer lock head and before that we had ‘done’ two caissons for a project in Hamburg. But with a length of no less than 80 metres, a width of 55 metres and a height of 25 metres, the inner lock head was by far the largest one of the four. It is nice to see that we have grown into an experienced team. Despite the enormous size of the last caisson, we have managed to work very accurately. Although, at times, we had to improvise, for example, when we spent a lot of time finding the right type of lighting to get good CCTV images in the enclosed work space. What was so special about the inner lock head was that – due to the size of the caisson – we had to work with as many as four dredging arms. The dredging teams had to work in close cooperation so that the caisson would sink evenly and not list to one side. For this purpose, we drew up a new dredging plan every 12 hours. The sinking operation has been a great success. At present, we are still busy with the evaluation of the project and learning lessons for future caisson sinking operations.