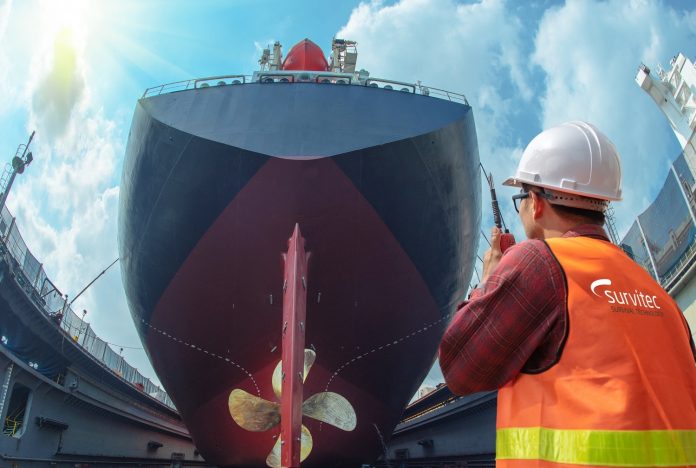
Survitec, a provider of Global Survival Technologies solutions, has created a new, formalised pre-inspection solution as part of its dry dock safety service to assist ship owners and managers in optimising and expediting dry docking timetables.
The pre-inspection service is designed to support the repair and inspection of all onboard safety and lifesaving equipment as part of Survitec’s fully managed, “safety-first” dry docking solution.
According to the statement, during routine port operations, a skilled service technician boards the ship to assess and verify the scope of work, with the added benefit of assisting in ensuring dry dockings do not overrun and ships leave on schedule, completely certified, and under budget.
“It smooths the entire dry-docking process,” stated Jan-Oskar Lid, Survitec technical sales manager.
He further added “A pre-inspection does not have to take place in the same yard or location where the dry dock will take place. This is the advantage of our global service station network.”
Another advantage stated by the company is that the new solution can lessen the danger of any unexpected work occurring during dry docking, which might result in unanticipated delays, increased costs, and lost income.
“Our trained technicians can identify issues that the ship owner or manager may not have yet recognised or may have been misdiagnosed. For example, one customer ordered a gas top-up for a CO2 low-pressure system. During a preparatory call, we were able to identify an underlying issue with the tank and arrange the necessary repairs. If this issue had not been identified until the time of service, the vessel could have been left off hire for longer, causing costly delays to their operating schedule,” explained Lid.