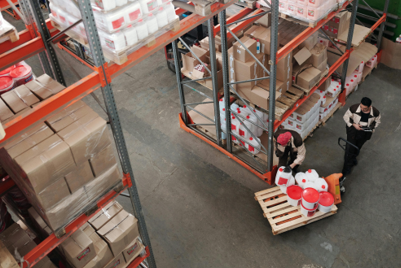
Photo by Tiger Lily on Pexels
When your warehouse space is well arranged, everything is readily accessible, wastage is minimized, and workflow is maximized. No matter how big or small your warehouse space is, the utilization of strategic organizational strategies can easily affect efficiency and also the performance of the staff. The following are five organizational concepts for warehouses that will ensure maximum productivity and ease operations.
1. Implement a Clear Labeling System
Simple and straightforward labeling makes all products visible and accessible. The most common types of product identification are bar codes, QR codes, and alphanumeric marks. Proper labeling and labeling on bins, racks, and shelves saves employees time scanning around and expedited orders ship out quicker.
Tags should be durable and readable, particularly for the high-traffic areas. Additionally, color-code areas by department or types of products. This reduces confusion, is easy to train workers, and helps control inventory more effectively across the warehouse.
2. Train Staff to Keep the Area Organized
Even the best organizational system can fail without proper upkeep. Proper training of your warehouse employees in keeping things in order is just as necessary as putting the initial framework in place. Your staff must understand the rationale for your design and be reminded to put away tools, equipment, and inventory in their assigned location once used.
Consider partnering with companies like SchoolLockers to get storage supplies for employees. Individual storage can also promote responsibility and minimize clutter, making the workplace safer and more efficient.
3. Use Vertical Space Effectively
Every space counts for your warehouse efficiency, and there is a lot of potential in the overhead spaces. Positioning the high shelving units and using mezzanine floors offers much more storage without increasing the building footprint. The technique is very effective for storing slow-moving stock or bulk materials.
Ensure vertical storage systems are access-safe with forklifts or rolling ladders. Vertical organization of merchandise also saves floor space, reduces the complexity of moving materials, lessens disorganization of workflow, and avoids congestion in crowded areas.
4. Optimize Pick Paths
An optimized route ensures that employees walk less and have more time for fulfilling orders. Verify your warehouse floor plan to have merchandise stored in an optimal travel distance. Stock high-volume items close to packing stations to reduce steps and lost time.
Implementation of a warehouse management system is instrumental in automating the most optimal pick routes based on historical data. While reducing picking errors, it also increases throughput and decreases labor costs in the long run. The route should be audited and updated periodically, depending on order behavior, as a measure critical to ensuring efficiency.
5. Conduct Regular Inventory Audits
Periodic counting assists in maintaining the appropriate levels of inventory and uncovering organizational inefficiencies. Cycle counting wherein, small quantities of the inventory are counted regularly, can reduce disruption but still provide control over inventory accuracy. It assists in locating misplaced inventory or discrepancies before they become full-blown issues.
Apart from enhancing the accuracy of information, audits also guide on slow-moving or excess stock, which may be rotated or discounted. Auditing weekly or biweekly sets a culture of routine and accountability, which is more than well in tune with productivity goals.
Endnote
A well-organized warehouse guarantees efficiency in the flow of goods while curbing delays. It’s essential to stick to the best habits, including accurate inventory records and training workers. These practices result in streamlined operations, paving the way for the performance of the warehouse.